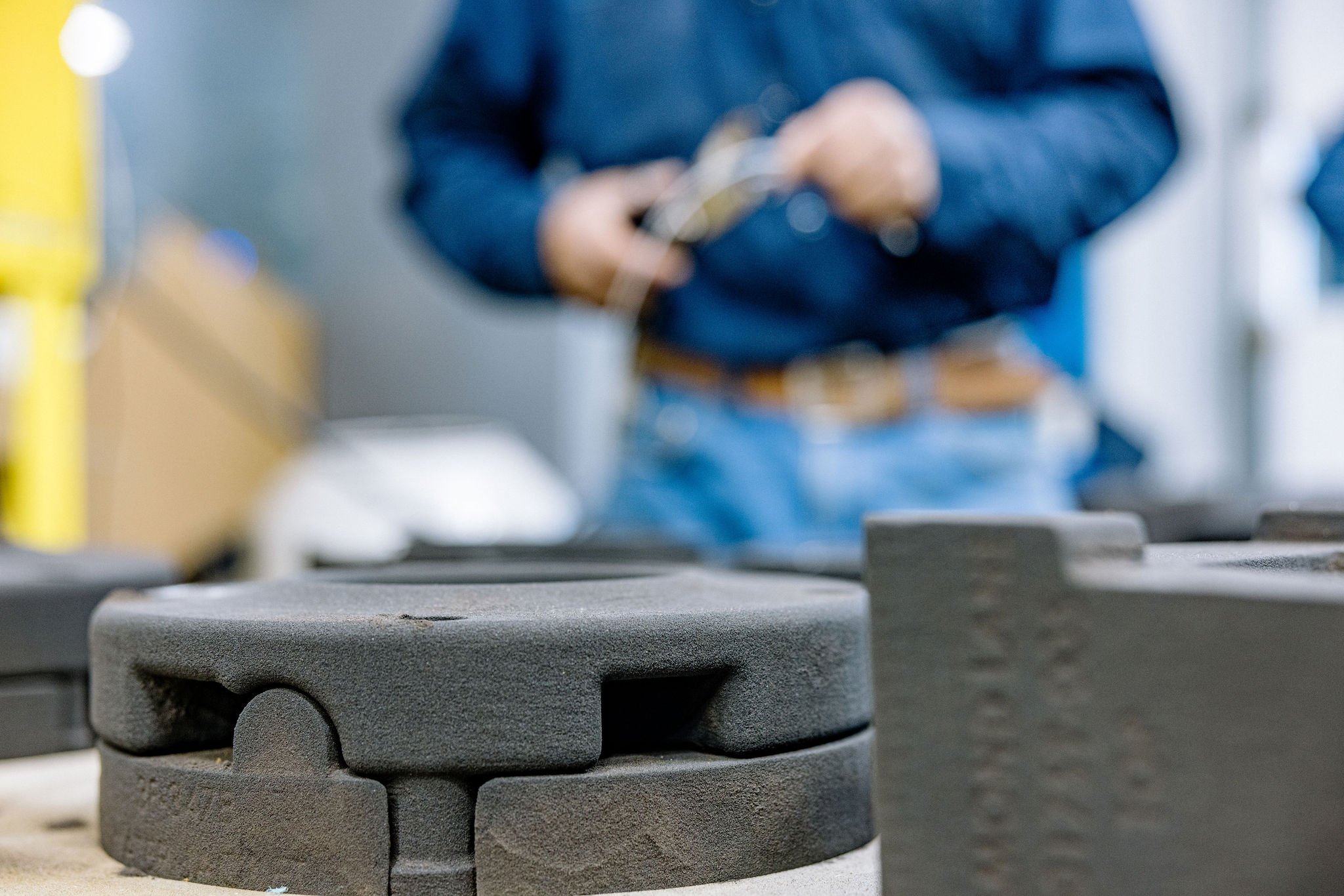
Consultations & Design
Your Part. One Time. Done Right.
At One-Off Castings, we don’t just pour metal—we build confidence from the ground up. Whether you're developing a prototype, replacing a legacy part, or crafting a unique component that won’t see a second run, our Consultations & Design service is tailored specifically for the challenges and nuances of one-off castings.
Every project is unique. So is our approach.
What It Is
One-off castings are custom, low-volume cast metal parts—designed to meet specific needs where no standard solution exists. These projects often involve:
Legacy or discontinued parts
Early-stage product development
Specialty components for aerospace, industrial, or defense applications
Repair or replacement parts with no blueprint
Our team partners with you from day one to ensure your one-time part is designed for success—technically sound, cost-effective, and built to perform.
How It Works
Our Consultation & Design process is hands-on, highly collaborative, and built to de-risk the casting process before any tooling or pouring begins.
Step 1: Technical Consultation
We’ll start by reviewing your part needs, specs, or existing models. Our engineers evaluate geometry, stress points, potential hot spots, and recommend optimal materials and casting methods for a one-off run.
Step 2: Engineering & Simulation
Using advanced solidification modeling software, we simulate the casting process digitally. This allows us to:
Visualize how molten metal will flow and cool
Predict shrinkage, gas porosity, or distortion
Adjust riser and gate design to ensure structural integrity
Step 3: Design Optimization
With insights from simulation, we refine the 3D model for improved castability and performance. We also plan for post-casting processes like machining or heat treatment—critical when your part only gets one shot.
The Power of Solidification Engineering
Unlike high-volume production, one-off castings can’t afford trial-and-error. That’s why our investment in solidification and flow simulation tools pays off.
These technologies allow us to:
Eliminate internal defects before they happen
Reduce lead times and scrap
Ensure quality on the first pour
Our engineers combine deep foundry experience with modern design tools to bring a level of precision rarely offered in single-part projects.
Why It Matters
With one-off castings, there are no second chances.
That’s why our design-first approach is essential:
No wasted time. Every decision is intentional.
No guesswork. Every part is engineered with simulation.
No compromises. Every project is supported by real technical expertise.
When you only need one—and it has to be right—our consultation process ensures you get exactly what you need, without the risk of going it alone.
Ready for Your One-Off?
We specialize in one-of-a-kind castings—and that specialization starts at the design table. Let us walk with you from concept to casting with confidence and clarity.